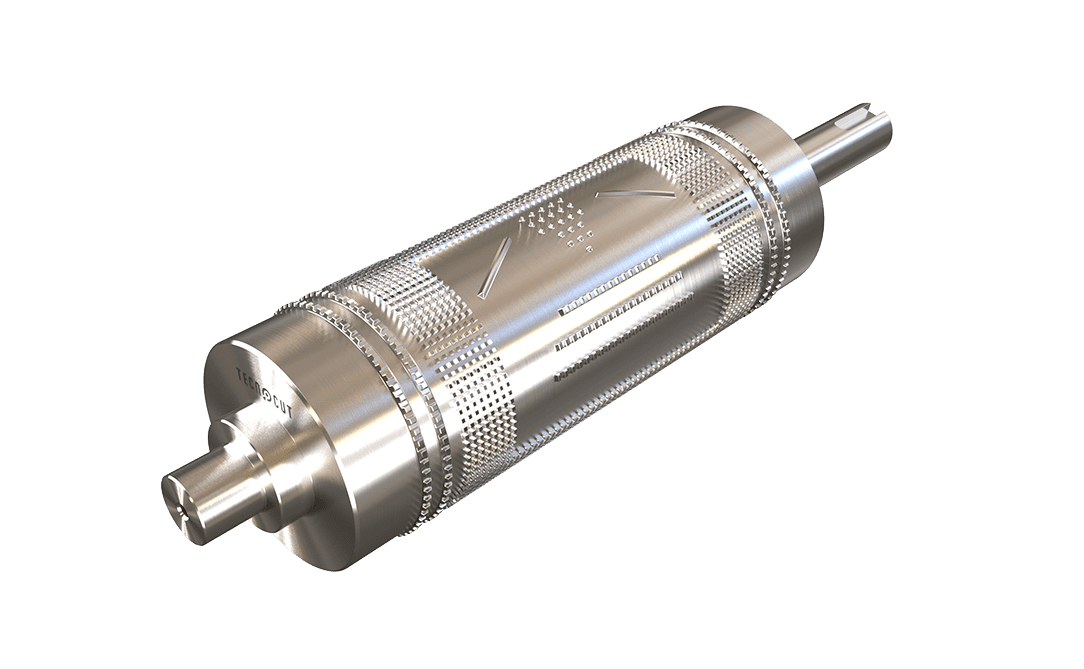
Focus on maximum quality
Ultrasonic welding
Take your productivity to the maximum
The ultrasonic welding cylinders for the production of surgical masks can be adapted to any type of rotary machine.
- It helps to achieve very good results results in terms of strength, tightness, and visual appearance.
- The resulting friction heat melts the material directly at the joining points of the individual material layers.
- Because of low energy consumption, the material undergoes very little thermal stress.
Advantages of working with ultasonic welding
Get the best results
Higher performance
Allows high-volume production in the textiles, medical, hygiene, filter, and general technical industries
100% adaptable
Ultrasonic welding systems (or ultrasonic modules) can also be easily integrated into production lines.
High quality
If the combination of materials, the anvil profile, and the ultrasonic system are appropriately designed.
Save costs
Ultrasonic welding enables to work on high speed, while saving energy and avoiding production downtime.
Applications of the ultasonic welding
Discover everything you can do
When welding nonwovens in combination with longitudinal seals, high-strength connections are established at the joint areas. Rotary ultrasonic systems are particularly suitable for joining applications in marginal areas.
Benefits / special features:
- Additional web material transport
- Fast processing
- Tight and strong connection
When welding cross seals, instantaneous peak power must be precisely controlled and introduced into the joint areas in a minimum of time. For such applications, correct selection of the anvil geometry and the ultrasonic system is of particular importance.
Benefits / special features:
- Consistent and uniformly strong connection
- High product throughput per minute
- Soft hand feel
Targeted joining of several layers of nonwovens by means of ultrasonics and an anvil drum with structure. Bonding of the material web is merely performed in “spots”, which prevents any adverse effects e.g. on filter properties or stretching behavior of elastic composites.
Benefits / special features:
- Energy-saving
- No adhesives required
- Fast processing
- Textile hand feel is maintained
- Low energy consumption
- Color designs possible without additional print
- High process speeds
- Process control
- Fiber-free perforation
- Fiber-free welding of cutting edges
- High production speeds
- Material splices in end product-quality